The Role of CNC Technology in Achieving Manufacturing Accuracy
- sanshiaerotech
- Jun 19
- 4 min read
CNC (Computer Numerical Control) technology has transformed the manufacturing industry, enabling companies to achieve remarkable levels of accuracy and precision. In the age of automation, manufacturers are increasingly relying on CNC machines to streamline their operations, reduce human error, and enhance the quality of their products. This blog post delves into the significant role CNC technology plays in achieving manufacturing accuracy and the benefits it offers.
Understanding CNC Technology
CNC technology refers to the automated control of machining tools by means of a computer. Unlike traditional machining, which often involves manual labor and mechanical adjustments, CNC machines operate through programmed commands that dictate the movement of tools and machines. This technology is applicable in various forms including milling, turning, and grinding.
One of the key advantages of CNC technology is its ability to replicate designs with high fidelity. Once a design is inputted into the CNC machine, it can process the command repeatedly without deviating from the intended dimensions. This consistency ensures that the final products are uniform, which is crucial in industries such as aerospace, automotive, and medical device manufacturing.
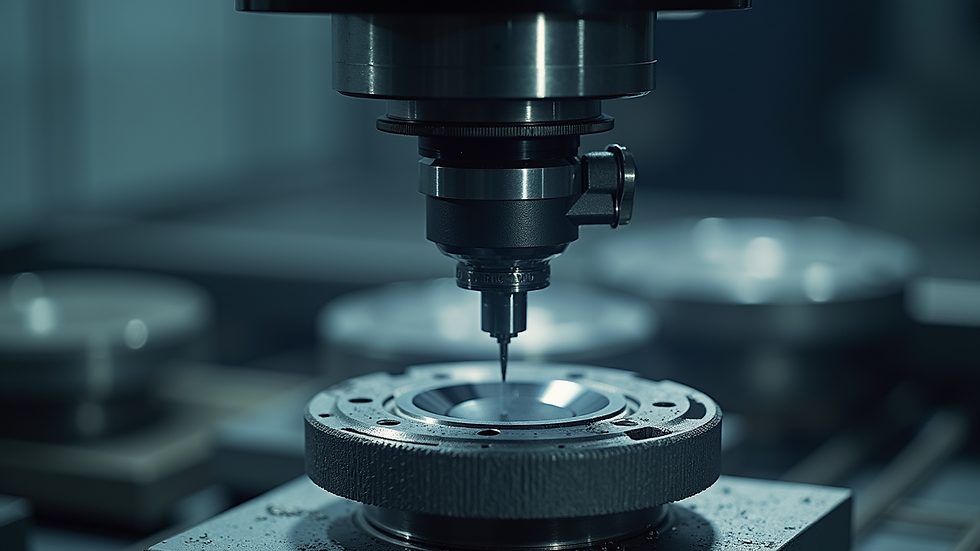
The Importance of Precision in Manufacturing
Precision is paramount in manufacturing. It not only affects the quality of the final product but also influences costs, efficiency, and safety. Inaccurate parts can lead to assembly problems, increased wastage, and even safety hazards in certain applications.
Statistics reveal that a significant percentage of manufacturing defects stem from human error. A study showed that 20% of manufacturing costs can be attributed to mistakes made during the machining process. By embracing CNC technology, manufacturers can greatly reduce this risk, leading to better quality control and ultimately fewer recalls or defects.
Benefits of CNC Technology
Increased Efficiency: CNC machines operate faster and with more accuracy than their manual counterparts. This efficiency leads to shorter lead times and increased output, which is vital in a competitive marketplace.
Cost-Effectiveness: While the initial setup of CNC machines may be expensive, the long-term savings are substantial. Reduced material waste and less labor cost due to automation contribute to lower overall production costs.
Scalability: CNC technology allows manufacturers to scale up production without compromising quality. Once a machine's program is established, it can produce large quantities of identical parts without fatigue or error.
Complex Design Capabilities: CNC machines can produce intricate designs that traditional machining techniques may struggle to replicate. This flexibility in design opens up new possibilities for innovation in product development.
It is evident that CNC technology is an essential element in the drive towards achieving higher manufacturing accuracy and efficiency.

How much does CNC machining cost per hour?
The cost of CNC machining can vary greatly depending on several factors, including the complexity of the project, the type of materials used, and the specific CNC machine operation being performed. On average, CNC machining costs can range from $75 to $150 per hour.
For example, basic machining tasks such as milling or turning might fall on the lower side of that range, while more complex operations involving precision parts or specialized processes may push costs higher. Additionally, the costs may also include setup fees, tooling charges, and material costs. It is advisable for manufacturers to obtain detailed quotes from service providers to fully understand the cost structure associated with their projects.
The Future of CNC Technology
As technology progresses, we can expect to see even greater advancements in CNC technology. Innovations such as machine learning and artificial intelligence are starting to make their way into CNC machining, which could further enhance accuracy and efficiency. Predictive maintenance capabilities can reduce downtime by anticipating equipment failures before they occur, ensuring continuous operations and sustained productivity.
Moreover, the integration of IoT (Internet of Things) with CNC machinery is paving the way for smart manufacturing environments. Machines will be able to communicate performance data in real-time, allowing manufacturers to make informed decisions on operations, energy usage, and production schedules.
In terms of sustainability, CNC technology also offers the possibility of reducing waste, as it optimizes material usage and minimizes errors. This not only benefits the environment but also ensures that companies remain competitive in an increasingly eco-conscious market.

Implementing CNC Technology in Your Operations
For businesses considering the switch to CNC technology, proper planning and training are vital. Here are some actionable recommendations:
Invest in Training: Employees need to be trained to operate CNC machines effectively. Regular workshops and hands-on training sessions can enhance their skills and improve productivity.
Select the Right Equipment: Depending on your specific needs, invest in CNC machines that cater to your operational requirements. Consider factors such as size, precision levels, and software compatibility.
Partner with Experts: Collaborating with service providers offering cnc machining services can help in better understanding the machining landscape. They can offer valuable insights and expertise that can streamline your operations.
Regular Maintenance: Implementing a routine maintenance schedule is crucial for ensuring the longevity and reliability of CNC machines. Regular checks can prevent unexpected breakdowns and costly repairs.
Embrace Innovation: The technology landscape is continually changing, and it is essential to stay updated with the latest innovations and trends in CNC machining. This will enable businesses to seize new opportunities and maintain a competitive advantage.
While CNC technology has already made significant strides in improving manufacturing accuracy, there is still room for growth and enhancement. The integration of new technologies will lead to even more innovative applications, pushing the boundaries of what is achievable through CNC machining.
In conclusion, CNC technology is important in achieving accuracy and consistency in modern manufacturing processes. As industries continue to evolve, those who adopt and integrate CNC technology will not only improve their operational efficiency but also lead the way in producing high-quality products that meet the demands of today's market.
Comments